Selecting an ideal rewinder machine is crucial to manufacturers operating in high-speed and precision environments. A well-selected rewinder ensures consistent product quality while also optimizing throughput, minimizing downtime, and prolonging equipment lifespan. This paper-style article offers an in-depth examination of material-specific rewinder selection, covering topics like:
- Material Characteristics & Rewinder Compatibility
- Key Machine Features in Multi-Material Rewinding Systems
- Machine Configuration Strategies & Modulus of Elasticity Compatibility
- Empirical Case Studies
- Production Line Integration for Material-Specific Order Fulfillment
1. Material Characteristics & Rewinder Compatibility
Every substrate has unique chemical and physical properties. These affect tension, handling and winding. It is important to understand these properties in order to ensure rewinder compatibility and prevent defects like web breaks, wrinkles or delamination.
1.1Paper and paperboard papers’ inherent porosity and moisture sensitivity require precise tension control settings, especially with hygroscopic materials like biodegradable PLA. An insufficient tension setting can result in uneven winding, while too much tension increases fiber tearing risk. Mandrel selection depends on core diameter and roll weight. Air shafts offer quick roll changeovers, while mechanical chucks offer stronger clamping of heavy rolls; surface finishes and coatings need nip rolls to keep their gloss without leaving markings behind.
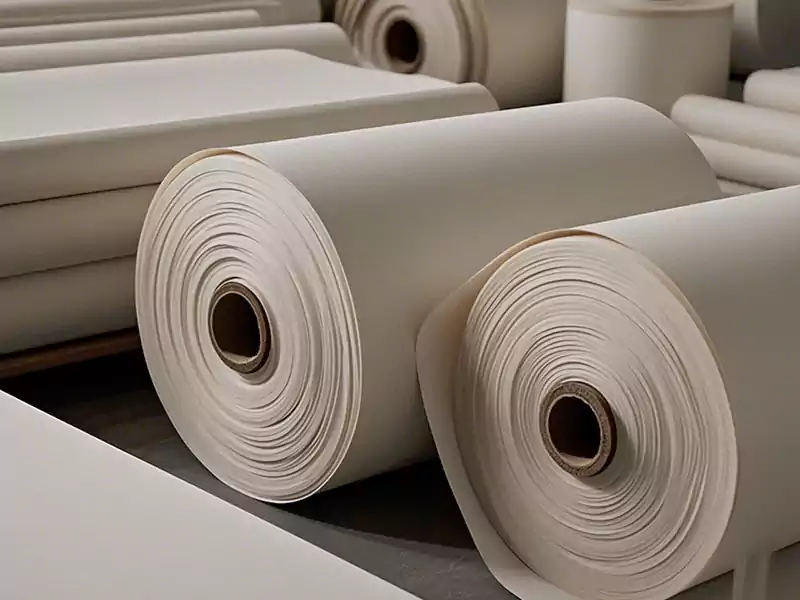
1.2 Plastic films (PE, PP and PET), due to their elastic modulus and stretchability characteristics differing between BOPP and metalized PET varieties, require different tension control settings. Electronic tension systems utilizing load cells with torque feedback enable real-time adjustments that help minimize web breakage; ultrathin PVDF films benefit from microtension oscillation controls coupled with real-time thickness gauge feedback loops to dynamically modulate tension depending on gauge fluctuations; static charge accumulation is reduced using anti-static bars and ionizing systems while adhesive activation during winding guarantees clean splices when high tack adhesives are utilized for robust splicing applications;
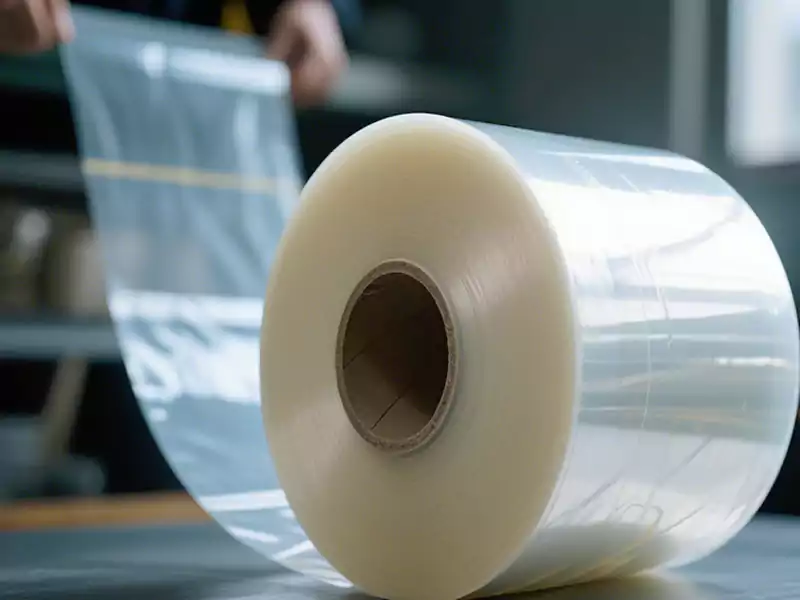
1.3 Plastic films (PE, PP and PET), due to varying elastic modulus and stretchability characteristics between BOPP and metalized PET varieties, require different tension control settings. Electronic tension systems with load cells equipped with torque feedback enable real-time adjustments that help minimize web breakage; ultrathin PVDF films benefit from microtension oscillation controls coupled with real-time thickness gauge feedback loops to dynamically modulate tension according to gauge fluctuations; static charge accumulation is reduced using anti-static bars or ionizing systems while adhesive activation during winding ensure clean splices when high tack adhesives are employed splicing applications.
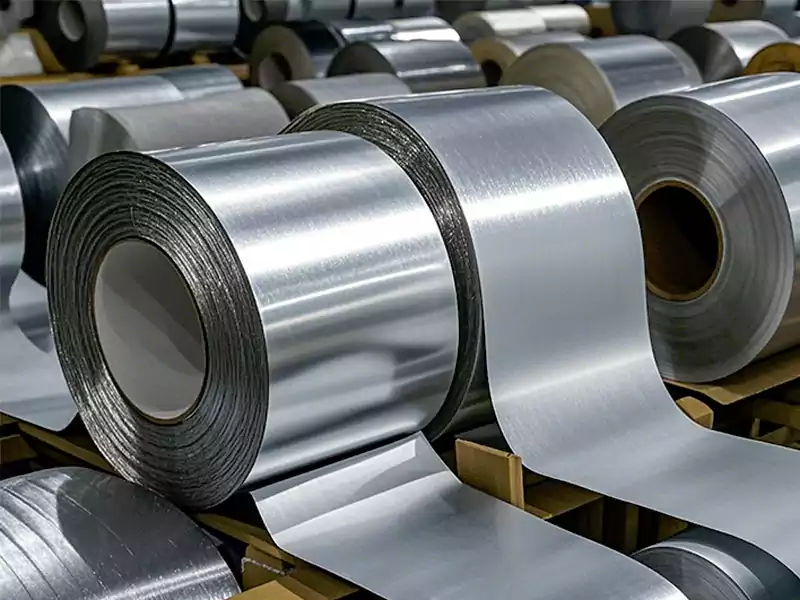
2. Key Machine Features in Multi-Material Rewinding Systems
A versatile rewinder must accommodate rapid transitions between substrates, embodying the principles of multi-material rewinding systems. The following features are essential:
2.1 Advanced Tension Control
Electronic vs Mechanical Systems: When switching between stiff paperboard and elastic films, electronic tension control using load cells and torque feedback offers superior accuracy to mechanical brakes.
Microtension Oscillation Controls: Used with ultrathin PVDF films and high-tack adhesive applications, these controls apply microadjustments at high frequencies in order to avoid web flutter and maintain even roll density.
2.2 Precision Web Guiding & Alignment
Edge and Center Guides: Mechanical edge guides offer lateral stability while center guides allow variable width webs.
Non-Contact Sensors: Ultrasonic and optical sensors offer gentle guidance of delicate substrates.
Real-Time Thickness Gauge Feedback Loops: These closed-loop systems use thickness measurements to constantly adjust guide position and tension, ensuring consistent winding regardless of gauge variations.
2.3 Automated Splicing & Roll Changes
Splicing Methods: Manual splicing is suitable for low-volume runs, semi-automatic systems balance speed and cost, and fully automatic splicers eliminate operator intervention, reducing waste.
Turret Rewinders & Dual-Shaft Systems: These configurations allow one roll to unwind while the other rewinds, enabling seamless roll changeovers and maximizing uptime.
2.4 Throughput & Speed Management
Minimum Rewinder Speed for High-Tack Adhesives: Speeds of 50–100 m/min ensure adequate dwell time for adhesive activation without risking slippage.
Acceleration Profiles: Gradual acceleration and deceleration curves protect web integrity, especially for thermo-sensitive labels and embossed PVC sheets.
2.5 Safety & Maintenance Considerations
Emergency Interlocks: Immediate stoppage on sensor triggers prevents accidents.
3. Machine Configuration Strategies & Modulus of Elasticity Compatibility
To avoid slippage or overstretching, machine components such as shafts, rollers and brakes must be aligned with the material’s modulus of elastic compatibility.
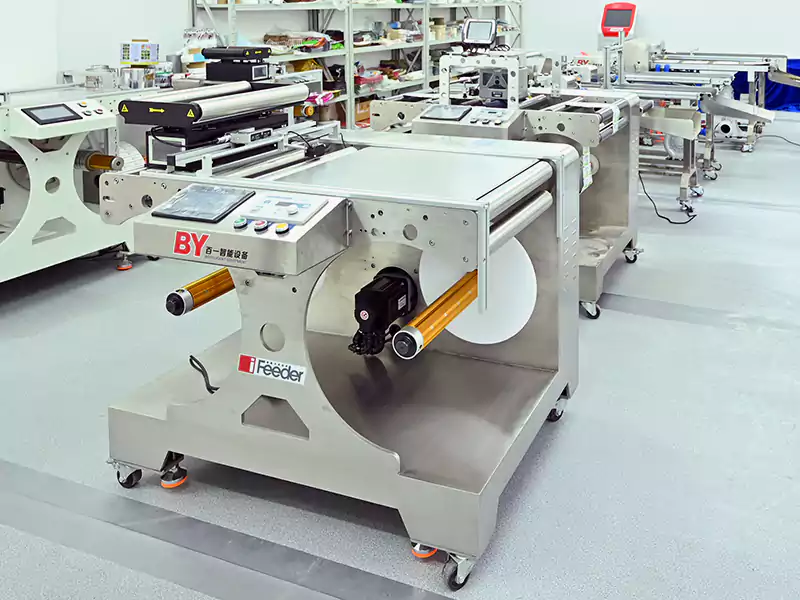
3.1 Core & shaft selection: air shafts, expanding shafts, and friction shafts offer different clamping forces and changeover speeds. Air shafts excel in high-speed environments, while friction shafts provide continuous, adjustable pressure for materials with variable thickness, such as embossed PVC.
3.2 Roller surface materials selecting roller coverings—rubber, polyurethane, or Teflon—depends on substrate friction coefficients. Non-marking surfaces are mandatory for reflective foils and coated papers.
3.3 Environmental controls hygroscopic materials, including biodegradable PLA, require humidity-controlled enclosures to maintain consistent moisture content. Temperature-controlled nip rolls prevent thermal deformation of thermo-sensitive labels.
4. Empirical Case Studies
4.1 ABC Paper Co. utilized an electronic tension-control system and optical web guidance, leading to a decrease of 30% in web breakages among high-porosity boards.
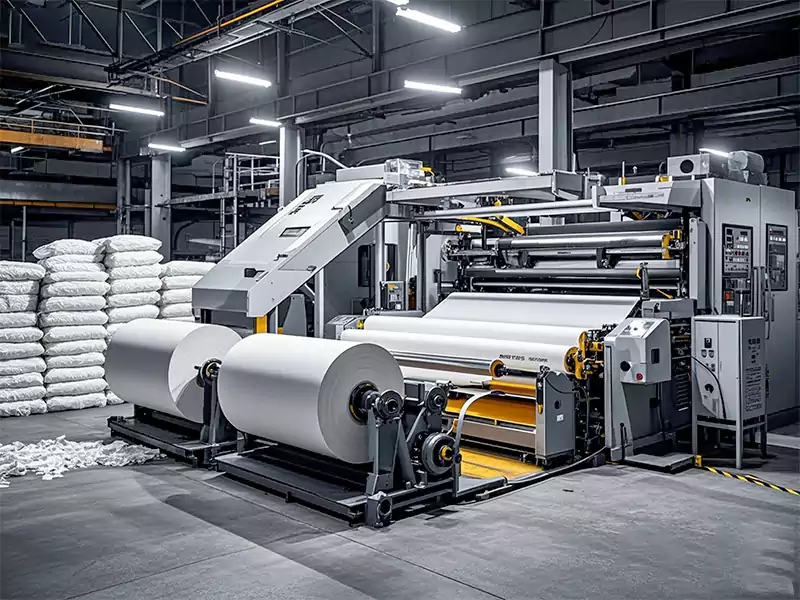
4.2 Films Ltd. installed a High-Speed Film Rewinder that features a dual shaft turret reel equipped with automatic adhesive and splicing activation to increase BOPP film throughput by 20% while keeping waste levels below 0.5%.
5. Production Line Integration for Material-Specific Order Fulfillment
Integrating a rewinder into an overall production line requires careful attention to both upstream and downstream processes to ensure seamless handling of various material types, while simultaneously increasing the flexibility and responsiveness of production systems to shifting order demands.
5.1 Modern rewinders are equipped with the capability of communicating with ERP & MES Systems, enabling real-time job tracking. Pre-programmed material recipes, tension profiles and roll dimensions based on order data facilitate quick changeovers while eliminating human errors and speeding job tracking.
5.2 Modular line architecture permits for flexibility of substrate type and order size by moving or bypassing rewinders as necessary. Mobile frames with quick-connect utilities enable flexible handling of different substrate types and order sizes.
5.3 By integrating sensors into a line and controlling its operation, dynamic adjustments can be made to match material behavior with line conditions. This is particularly essential when dealing with materials with moisture-retaining properties or thermosensitive labels that can change with environmental fluctuations that impact winding parameters.
5.4 To prevent bottlenecks and ensure smooth operations, rewinders must be coordinated with processes upstream, such as printing or slitting. Communication protocols at high speeds and central control interfaces enable coordinated web alignment and speed adjustment.
5.5 Real-Life Integration Examples
Label Printing Line: An integrated rewinder equipped with a thermosensitive label printer allows inline winding of printed labels after printing is complete, using real-time information from the printer to dynamically adjust tension according to print quality and adherent properties.
Label Printing Line: An integrated rewinder equipped with a thermosensitive label printer allows inline winding of printed labels after printing is complete, using real-time information from the printer to dynamically adjust tension according to print quality and adherent properties.
Pharmaceutical Packaging Line: Rewinders are installed after embossing units and coders to handle embossed PVC stock and tamper-evident label stocks. Microtension control systems help ensure consistent quality on sensitive substrates while maintaining traceability.
Conclusion
The selection of a material-specific rewinder is based on an understanding of the substrate’s properties, sophisticated machine features and precise configuration strategies. Integrating multi-material capability, ensuring compatibility with moduli, and using real-time control systems can help manufacturers achieve superior quality products, improved operational efficiency and increased throughput.
Next Steps: Conduct a detailed audit of your materials and process requirements, then engage with equipment specialists to specify a rewinder machine that aligns with your production goals and material portfolio.