Selecting an appropriate rewinder machine is critical for manufacturers operating in high-speed, precision-driven environments. A well-chosen machine not only ensures consistent product quality but also optimizes throughput, minimizes downtime, and extends equipment lifespan. This paper-style article provides an in-depth exploration of material-specific rewinder selection, addressing:
- Material Characteristics & Rewinder Compatibility
- Key Machine Features in Multi-Material Rewinding Systems
- Machine Configuration Strategies & Modulus of Elasticity Compatibility
- Empirical Case Studies
- Production Line Integration for Material-Specific Order Fulfillment
1. Material Characteristics & Rewinder Compatibility
Each substrate—paper, film, foil—exhibits unique physical and chemical properties that influence tension, handling, and winding behavior. Understanding these characteristics is foundational for ensuring rewinder compatibility and preventing defects such as web breaks, creases, or delamination.
1.1 Paper and paperboard paper’s inherent porosity and moisture sensitivity demand precise tension control settings, particularly for hygroscopic materials like biodegradable PLA. Inadequate tension can lead to uneven winding, while excessive tension risks fiber tearing. Core diameter and roll weight further dictate mandrel selection—air shafts provide rapid roll changeovers, whereas mechanical chucks offer robust clamping for heavy rolls. Surface finish and coatings necessitate nip rolls to maintain gloss and prevent marking.
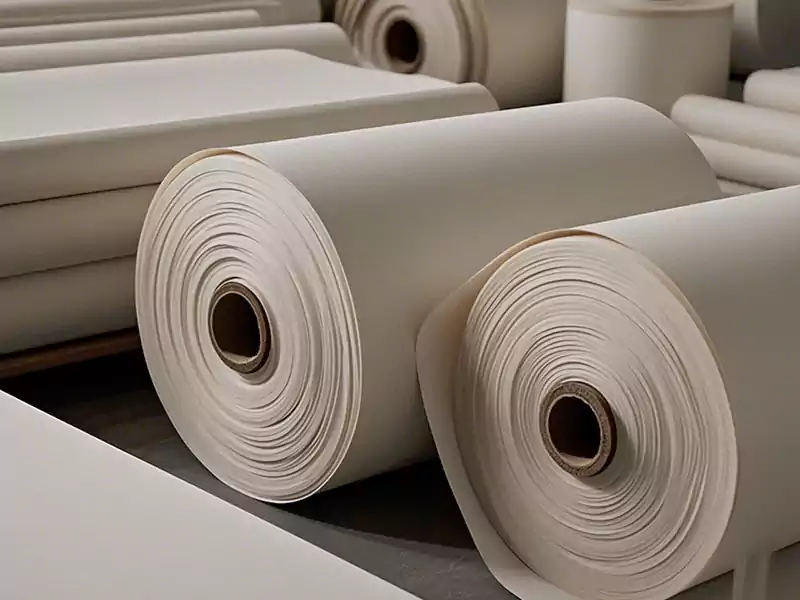
1.2 Plastic films (PE, PP, PET), the elastic modulus and stretchability of films such as BOPP versus metalized PET require differentiated tension control settings. Electronic tension systems leveraging load cells and torque feedback enable real-time adjustments, mitigating web breakage. Ultra-thin PVDF films benefit from microtension oscillation controls and real-time thickness gauge feedback loops, which dynamically modulate tension in response to gauge fluctuations. Static charge accumulation is addressed through anti-static bars and ionizing systems, while adhesive activation during winding ensures clean, robust splices when using high-tack adhesives.
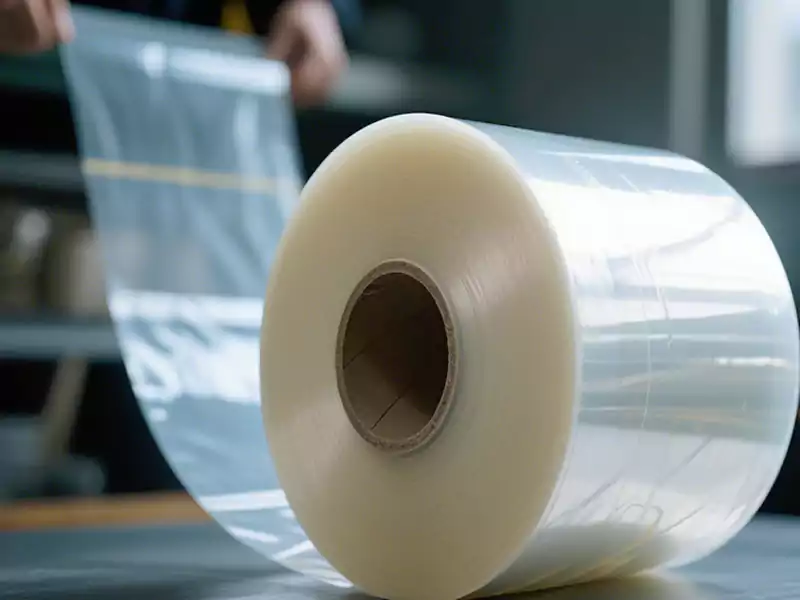
1.3 Foils (Aluminum, Metalized Films) are conductive and prone to static dissipation issues; proper grounding and static control mechanisms are mandatory to avoid sparks. Their low ductility and high reflectivity make them sensitive to creasing—low-tension rewinding combined with non-marking rollers preserves surface integrity. Film foil rewinder differences include the adoption of dual-shaft turret designs, which facilitate uninterrupted production via on-the-fly roll changes, and microtension oscillation controls for handling ultra-thin metallic layers.
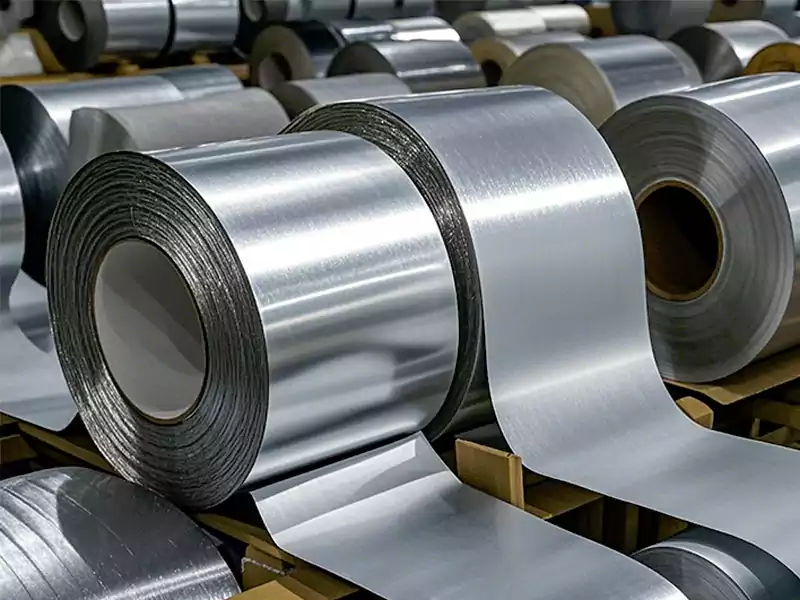
2. Key Machine Features in Multi-Material Rewinding Systems
A versatile rewinder must accommodate rapid transitions between substrates, embodying the principles of multi-material rewinding systems. The following features are essential:
2.1 Advanced Tension Control
Electronic vs. Mechanical Systems: Electronic tension control using load cells and torque feedback offers superior accuracy over mechanical brakes, particularly critical when switching between stiff paperboard and elastic films.
Microtension Oscillation Controls: Implemented for ultra-thin PVDF films and high-tack adhesive applications, these systems apply micro-adjustments at high frequency to prevent web flutter and maintain uniform roll density.
2.2 Precision Web Guiding & Alignment
Edge and Center Guides: Mechanical edge guides ensure lateral stability, while center guides accommodate variable-width webs.
Non-Contact Sensors: Ultrasonic and optical sensors facilitate gentle guiding of delicate substrates.
Real-Time Thickness Gauge Feedback Loops: These closed-loop systems use thickness measurements to continuously adjust guide position and tension, ensuring consistent winding across gauge variations.
2.3 Automated Splicing & Roll Changes
Splicing Methods: Manual splicing is suitable for low-volume runs, semi-automatic systems balance speed and cost, and fully automatic splicers eliminate operator intervention, reducing waste.
Turret Rewinders & Dual-Shaft Systems: These configurations allow one roll to unwind while the other rewinds, enabling seamless roll changeovers and maximizing uptime.
2.4 Throughput & Speed Management
Minimum Rewinder Speed for High-Tack Adhesives: Speeds of 50–100 m/min ensure adequate dwell time for adhesive activation without risking slippage.
Acceleration Profiles: Gradual acceleration and deceleration curves protect web integrity, especially for thermo-sensitive labels and embossed PVC sheets.
2.5 Safety & Maintenance Considerations
Emergency Interlocks: Immediate stoppage on sensor triggers prevents accidents.
3. Machine Configuration Strategies & Modulus of Elasticity Compatibility
Machine components—shafts, rollers, brakes—must align with the modulus of elasticity compatibility of the target material to avoid overstretching or slippage.
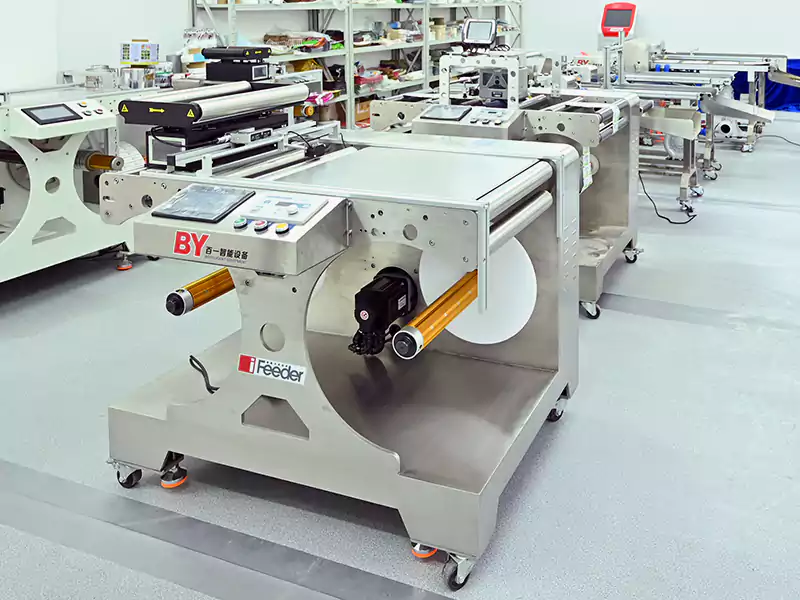
3.1 Core & shaft selection: air shafts, expanding shafts, and friction shafts offer different clamping forces and changeover speeds. Air shafts excel in high-speed environments, while friction shafts provide continuous, adjustable pressure for materials with variable thickness, such as embossed PVC.
3.2 Roller surface materials selecting roller coverings—rubber, polyurethane, or Teflon—depends on substrate friction coefficients. Non-marking surfaces are mandatory for reflective foils and coated papers.
3.3 Environmental controls hygroscopic materials, including biodegradable PLA, require humidity-controlled enclosures to maintain consistent moisture content. Temperature-controlled nip rolls prevent thermal deformation of thermo-sensitive labels.
4. Empirical Case Studies
4.1 Paper rewinding at ABC Paper Co.ABC Paper Co. integrated an electronic tension control system with optical web guiding, resulting in a 30% reduction in web breaks on high-porosity board and improved rewinder compatibility across multiple paper grades.
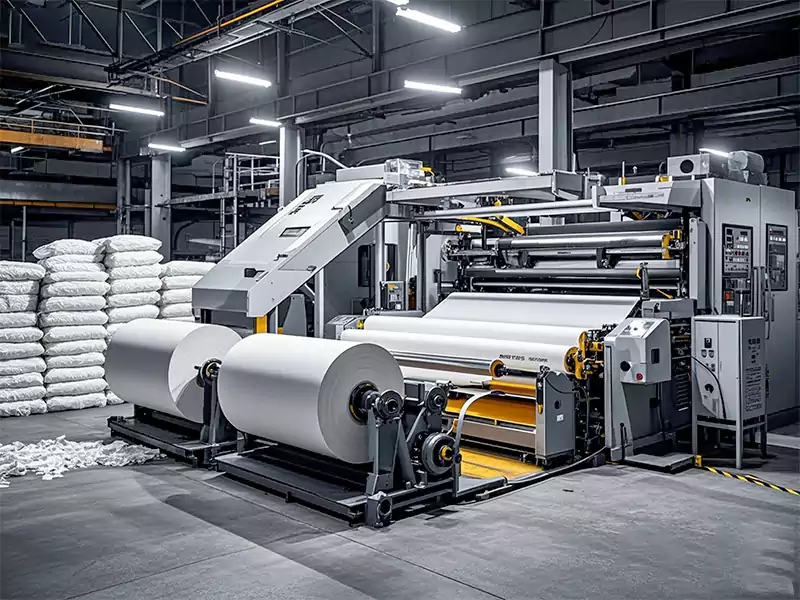
4.2 High-Speed Film Rewinder at Films Ltd. Films Ltd. deployed a dual-shaft turret rewinder featuring automatic splicing and adhesive activation during winding. The system achieved a 20% throughput increase on BOPP film runs while maintaining sub-0.5% waste rates.
5. Production Line Integration for Material-Specific Order Fulfillment
Integrating the rewinder into the broader production line requires careful consideration of upstream and downstream processes to ensure seamless handling of diverse material types. This approach enhances the flexibility and responsiveness of production systems to fluctuating order requirements.
5.1 Communication with ERP & MES systems, modern rewinders can be linked to Enterprise Resource Planning (ERP) and Manufacturing Execution Systems (MES) for real-time job tracking. Material recipes, tension profiles, and roll dimensions can be pre-programmed based on order data, streamlining changeovers and minimizing human error.
5.2 Modular line architecture adopting a modular configuration allows the rewinder to be repositioned or bypassed depending on the substrate. Quick-connect utilities and mobile frames provide the adaptability required for handling varying order sizes and substrates.
5.3 Real-time process adaptation integrating sensors and controllers throughout the production line, rewinder tension settings, speed, and nip pressure can be dynamically adjusted to match line conditions and material behaviors. This is particularly vital for hygroscopic materials and thermo-sensitive labels, where environmental shifts affect winding parameters.
5.4 Synchronization with printing and slitting operations to avoid bottlenecks, the rewinder must synchronize with upstream processes like printing or slitting. High-speed communication protocols and centralized control interfaces facilitate coordinated speed adjustments and web alignment, ensuring material integrity from start to finish.
5.5 Real-Life Integration Examples
Label Printing Line: A rewinder integrated with a high-speed label printer for thermo-sensitive labels enables inline winding immediately post-print. Using real-time feedback from the printer, tension is adjusted dynamically to preserve print quality and adhesive properties.
Flexible Packaging Film Line: A BOPP film printing and slitting line incorporates a turret rewinder with automated splicing, enabling roll changes without stopping the press. This setup supports rapid order changes and multi-design print runs without compromising film tension.
Pharmaceutical Packaging Line: Rewinders installed downstream of embossing and coding units handle embossed PVC and tamper-evident label stock. Integrated microtension controls ensure consistency in delicate substrates while preserving traceability features.
Çözüm
Effective material-specific rewinder selection hinges on a deep understanding of substrate properties, advanced machine features, and precise configuration strategies. By integrating multi-material capabilities, ensuring modulus compatibility, and leveraging real-time control systems, manufacturers can achieve superior product quality, operational efficiency, and sustainable throughput.
Next Steps: Conduct a detailed audit of your materials and process requirements, then engage with equipment specialists to specify a rewinder machine that aligns with your production goals and material portfolio.