Mobile connectivity is driving global industries. Manufacturers are under enormous pressure to package millions of SIM cards per day without compromising on quality. The use of manual feeding or pick-and-place robotics can create bottlenecks that lead to downtime, mistakes, and increased labor. Friction feeders are a gentle and reliable solution that uses continuous feed belts and controlled nip point separation. Packaging engineers can integrate these systems to synchronize the upstream preparation of cards with the downstream insertion, sealing, and labeling. This allows for new levels in efficiency and consistency.
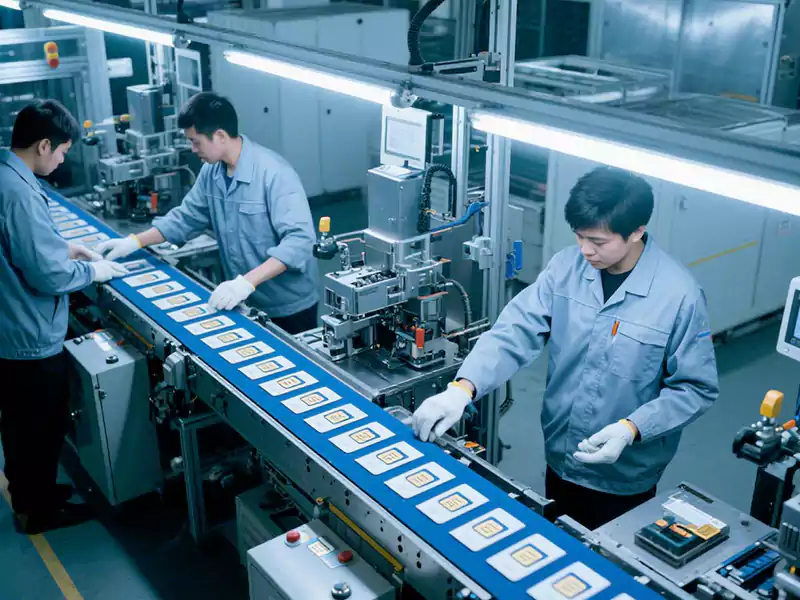
1. What is SIM packaging?
SIM packaging includes the materials, design, and processes used to package SIM cards, from manufacture through retail distribution. SIM packaging that is effective must: Protect electronic contacts against mechanical damage, moisture and dust.
- Automated singulation and feeding, without jamming.
- Printing data on the sleeves, blister cards, or cartons will help you to clearly brand your product, mark it with regulatory markings and track its origin.
- Include features that make it impossible to tamper with the package. This will assure regulators and end users of its integrity.
2. SIM Card Packaging Overview
We will explore below the common materials, formats and functional requirements as well as critical identifiers, such as the SIM number, that are central to modern packaging.
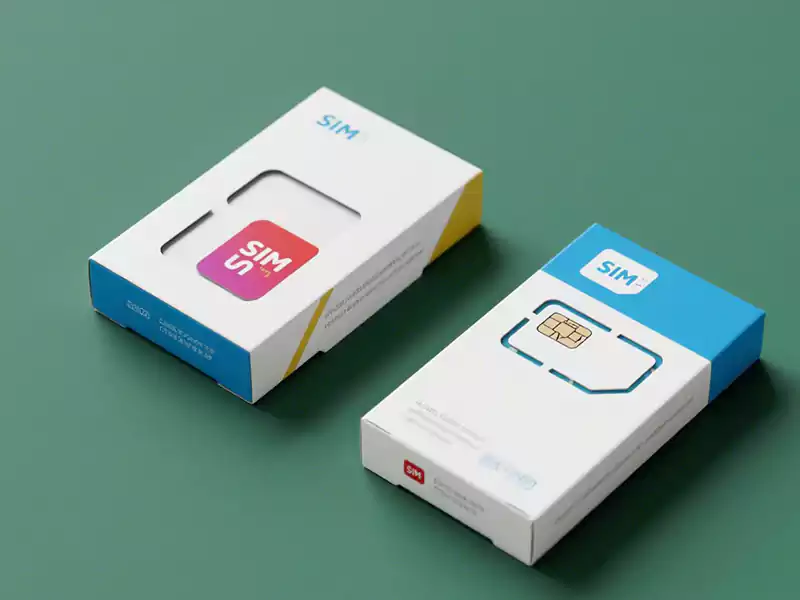
2.1 Materials & Components
- Thermoformed Films (PET/PVC ):
PET is transparent and stiff, making it ideal for retail displays. PVC is flexible but cost-effective. - Grades with high release prevent sticking when feeding at rapid, high speeds.
- Paperboard Sleeves & Wallets
- Paperboard, whether coated or uncoated, offers a durable surface that can be printed for branding and instructions.
Die-cut pockets house SIM cards, pins for ejectors and user guides securely in a slim profile. - ESD Dissipative Trays & Insets
Plastics that conduct electricity, like ABS with black carbon, can safely keep static away from sensitive contact points.
Used to arrange bulk stacks of cards before the final singulation. - Shock-Absorbing Foams:
Inserts of polyurethane or expanded polyethylene (EPE), which protect against mechanical shocks, are used during transportation.
2.2 Formats & Styles
- Face-Seal blister packs: Ideal for retail displays that require hanging film.
- Rigid Trays: durable PET trays with foil or hinged covers. Common for SIM kits and accessories.
- Paperboard wallets: A book-style packaging, with snap closures and printed instructions. Popular for eco-friendly or premium presentations.
- Bulk Cartons Corrugated boxes with ESD trays, or nesting paperboard packs, clearly labeled and barcoded.
2.3 Key Performance Criteria
- Orientation and Singulation: Cards should be placed face-up in the feeder, one at a time, without any overlap or skew.
- ESD protection: Ground metal guides and conductive straps prevent static accumulation on the feeder head.
- Seal integrity: Seals are subjected to a vacuum decay or visual inspection in order to protect against moisture or contamination.
- Tamper-Evidence: Tear notches, destructible sealings, or security foils reassure users and regulators about the integrity of packages.
2.4 Compliance & Quality Testing
- Mechanical stress tests: Simulated drop loads (1 m) or crush loads (>=500N) are used to ensure that packaging can withstand real-world handling.
- Dimensional accuracy: Vision systems check card position to within +-0.2mm in order to prevent misfeeds downstream.
- ESD audits: Periodic continuity and resistance checks confirm conductive pathways on trays and feeder components.
Regulatory Markings: CE, FCC and recycling symbols are printed to meet the global market’s requirements.
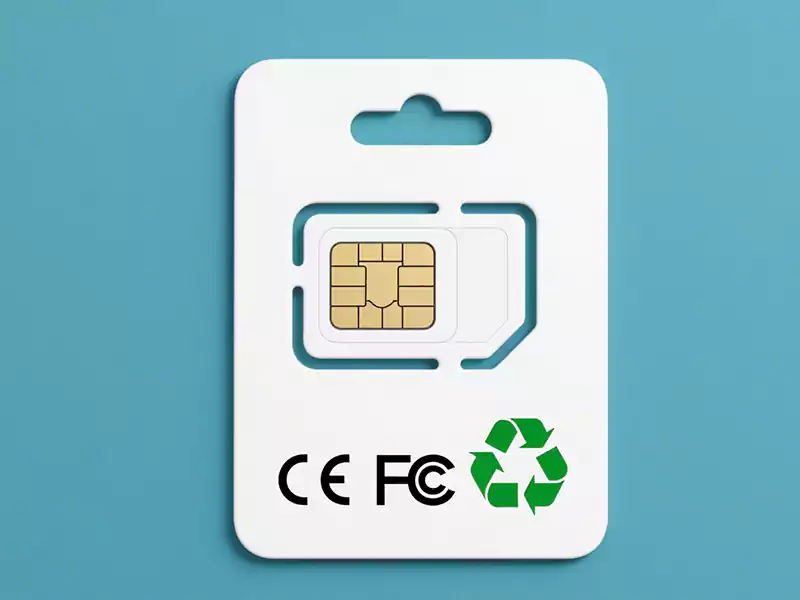
2.5 SIM card number on packaging
The ICCID (Integrated Circuit Card Identifier) is a unique identifier that’s printed on each packaged SIM card. This 19 to 20-digit number is:
- Uniquely identifies SIMs within cellular networks.
Appearance of barcodes and QR codes on bulk carton labels, paperboard sleeves or blister cards for scanning-based traceability. - The ICCID is etched or printed onto the SIM plastic body. This prevents mismatches when inventorying and activating the SIM.
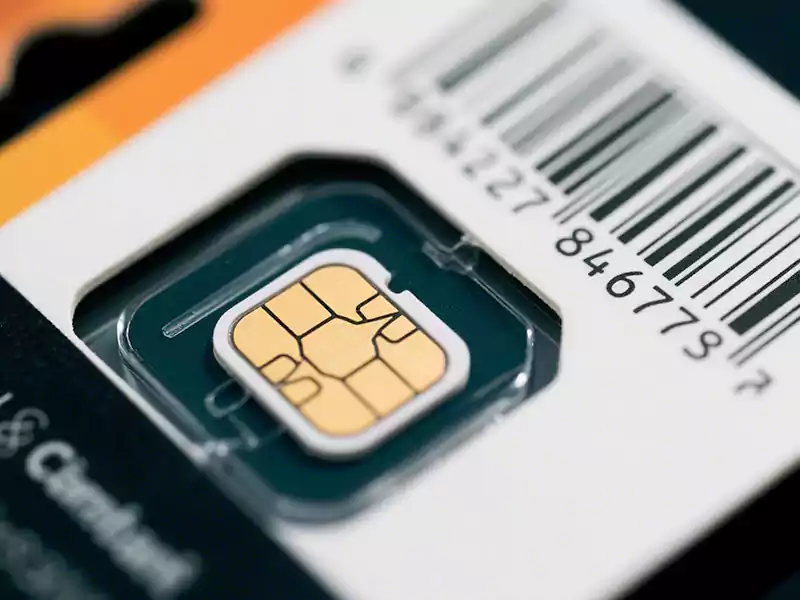
2.6 Sustainable Considerations
To reduce their environmental impact, manufacturers are increasingly choosing PET films, paperboard or biodegradable PLA. The use of lighter, thinner substrates reduces material costs, shipping weights and contributes to the circular economy.
3. SIM Card Lines: Features & Benefits
Friction feeders have a positive impact on SIM card packaging.
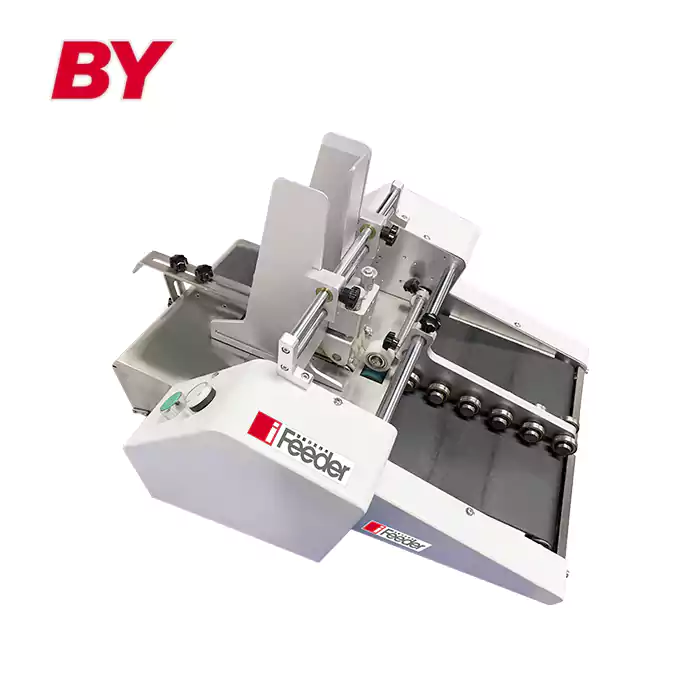
3.1 High-Speed, Continuous Feeding
Modern friction feeders achieve an average of 80- 100 ppm when it comes to standard SIM card thicknesses. The system maintains high productivity over long runs by eliminating the start-stop motion. This minimizes changeover delays and reduces operator intervention.
3.2 Alignment and Accuracy
The micro-adjustable guide plates and the feedback-driven roller force ensure that each card is centered before it enters blisters, sleeves, or cutting stations. This precision reduces downstream rejects by an average of 50-70 percent compared to systems that are intermittent.
3.3 Gentle, Contact-Friendly Handling
The uniform belt contact evenly distributes force over the card surface. This preserves delicate contacts and prevents edge chipping – a common failure mode in vacuum or gripper-based feeders.
5. Example in the Real World
After modifying the dual head friction feeding system, Liangcheng Electronics optimized the SIM card packaging line, eliminating the need for manual insertion of SIM cards into the packaging line, and effectively integrated them into the printing equipment, increasing the production capacity of its SIM card production line from 3000 sheets per hour to 4500 sheets per hour.
Friction feeders are the best solution for SIM packaging. They combine high-speed continuous feeding, micrometer-level accuracy, and gentle handling. The modular design of friction feeders, along with their advanced control systems and eco-friendly features, allows manufacturers to meet market demands while minimizing waste and maximizing uptime. Transform your SIM packaging line with friction-feeding technology. It will improve efficiency, quality, and sustainability.